鍛造ブロック・鋳造からAMへ・最適化設計の導入
ー熱交換器用バルブの事例ー
1. はじめに
今回ご紹介する事例は、2020年に実施された「Kansai-3D実用化プロジェクト」にて、Autodesk製品を選定された瀬尾高圧工業様の熱交換器用バルブへのジェネレーティブデザイン・積層造形活用です。
「Kansai-3D実用化プロジェクト」は、近畿経済産業局が展開するプロジェクトで、全国38社のモデル企業を対象に、国内外の3Dプリンタ関連企業27社、支援機関の協力のもと、3D製造プロセスに必要なデザイン・設計、3D造形、評価までのプロセスの導入検証を支援する日本初の取り組みです。

当プロジェクトにおいて、toDIM(当初toDMG)は、モデル企業様に対してAutodesk Fusion 360のジェネレーティブデザインを用いた3D積層造形に向けた支援を行いました。
2.課題・目標
瀬尾高圧工業様は、発電所や石油・ガス・化学プラントなどにに使われる各種鍛鋼品、各種プラント向けの熱交換器の製造、販売を行っている会社様になります。
今回対象となった製品は、鍛造品のバルブです。
特注の個別品の場合、品質とコストを考慮し、鍛造で製造されております。
本来、鋳造で製造し形を整えた形状になりますが、鍛造時は、ブロック形状で製造し、機能上必要な部分のみを切削加工されております。
加工性等を優先するため、
▲歩留まりが悪く、小ロットになると高価
▲鍛造ブロックの設計コストがかかる
▲ブロックになると重量としても非常に重く、軽ければ配管のサポートも低減できる
という現状がありました。
そこで、今回のプロジェクトでは、「質量の削減」「部品点数の削減」「体積の縮小」「開発プロセスの短縮」を実現するため、
●3DCADを活用し、最適化した形状を自社設計できるようになる
●製品の軽量化および製造工程の簡略化、AMの活用
を目標に活動を推進しました。
3.支援内容
今回のプロジェクトでtoDIMが提供した支援内容は下記になります。
①Fusion360の操作トレーニング
②ジェネレーティブデザインを活用した軽量化
③製造工程を考慮したリモデリング
④金属積層造形の支援
STEP1 Fusion360の操作トレーニング
「Kansai-3D」の趣旨の1つでもあった3D製造・設計プロセスを活用頂くために、まずは3D-CADのトレーニングからご支援させて頂きました。
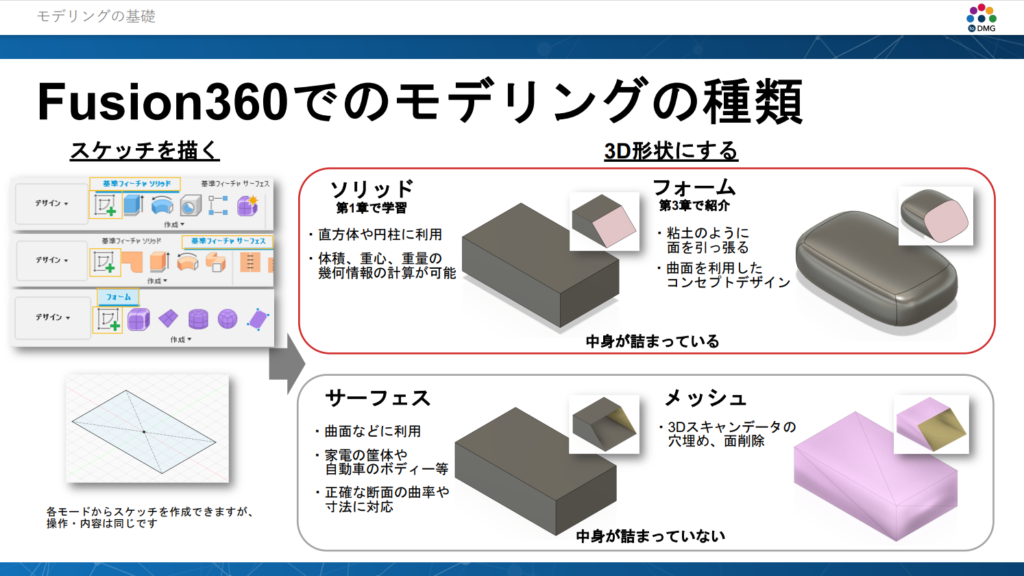
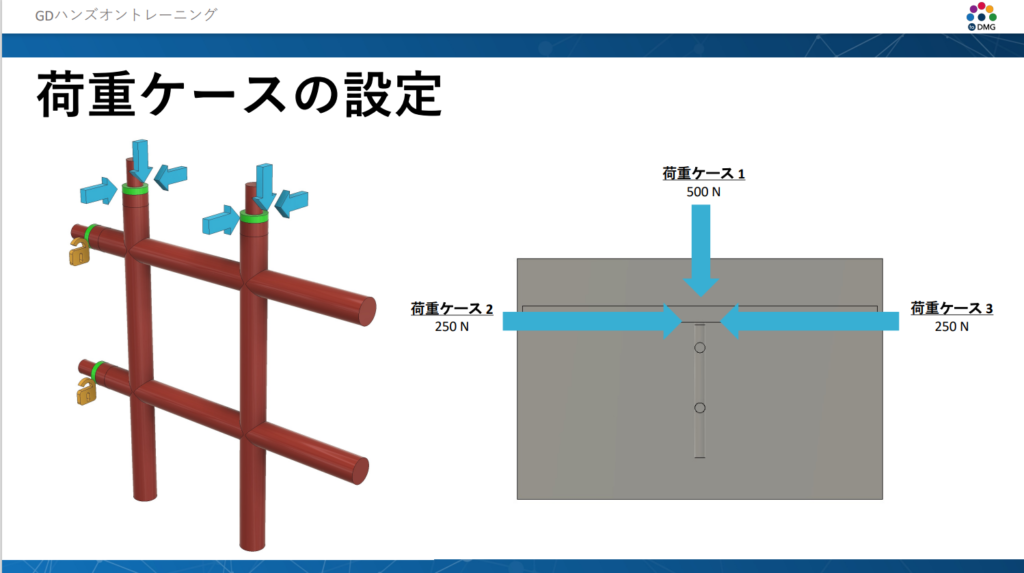
STEP2 ジェネレーティブデザインを活用した軽量化
また、最適化設計ツール「Fusion360 ジェネレーティブデザイン」の活用にあたり、実際の部品も見ながら、
・どの部分が本当に必要になるか(保持ジオメトリ、障害物ジオメトリの設計)
・荷重はどのくらい?どの方向から?(荷重条件、拘束条件の設計)
を検討し、ジェネレーティブデザインにて計算を行いました。
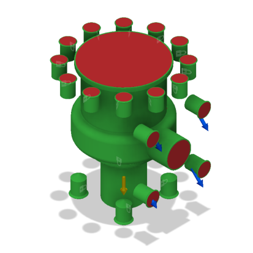
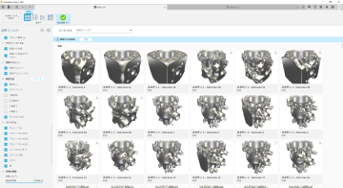
STEP3 製造工程を考慮したリモデリング
ジェネレーティブデザインで計算されたモデルはそのままでは造形困難な場合もあり、不要と判断できる細かな枝のよう形状や突状の部分は応力が溜まりやすいため、修正しました。
また対称でない形状となる場合もあります。
今回は円周形状であるため円対称になるようリモデリングを実施しました。
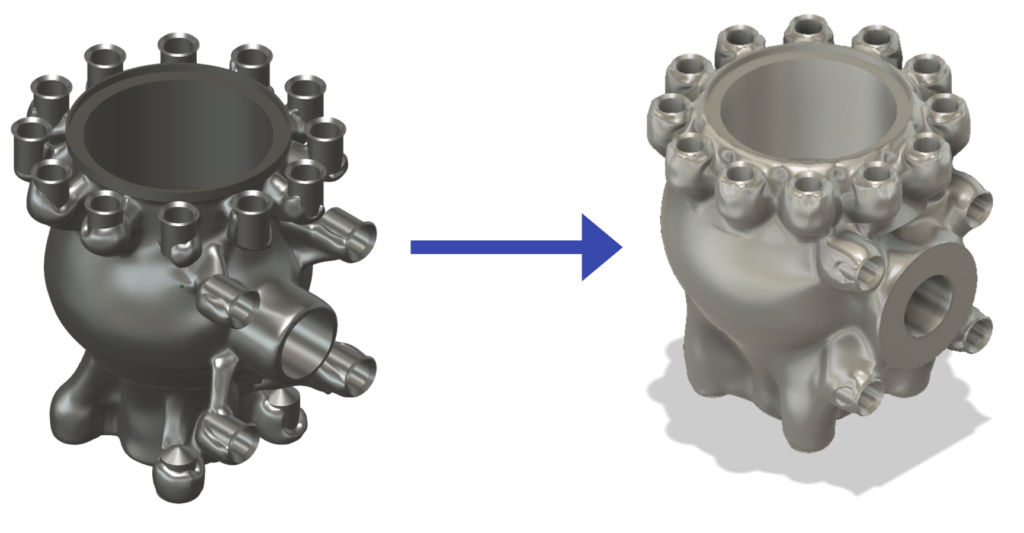
STEP4 造形
実際に造形した結果になります。
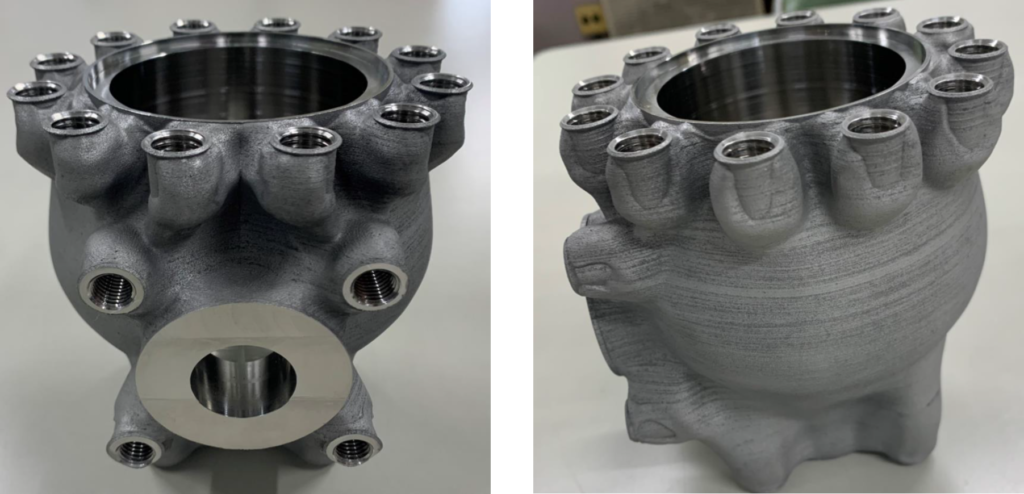
4.結果
今回、3D設計・ジェネレーティブデザインによる最適化設計および積層造形の活用により、
◎従来品と比べ、軽量化
◎切削加工と比べ、素材の廃棄量減少
が達成されました。
また、自社で3DCAD、AMを活用していくことにより、今後も他製品などへの適応可能性を探求されております。