事例:株式会社イメイド

EV車部品の軽量化へのAM活用
ーフロントバンパーブラケットの事例ー
1.はじめに
AM部品開発支援を活用されたのは、『株式会社イメイド』と『ものづくりネットワーク沖縄』が手掛ける、
電動モビリティの部品です。
電動モビリティは、”made in 沖縄”をコンセプトに車両開発・製造・販売まで手掛けている事業であり、
沖縄県の大型宿泊施設や観光施設などで実用化されています。
電動モビリティの航続距離を伸ばすことを計画しましたが、
アイデアを実現することが難しくtoDMGサービスを活用することになりました。
今回のプロジェクトでは、部品軽量化によるEV車両の電費延長を目的として部品開発を実施するとともに、
将来的なAMビジネスの可能性とAM技術の理解向上を目指した取り組みとなります。
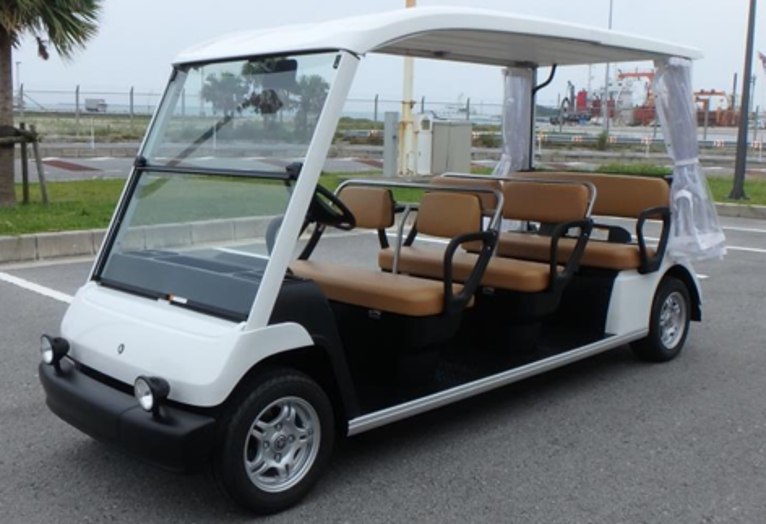
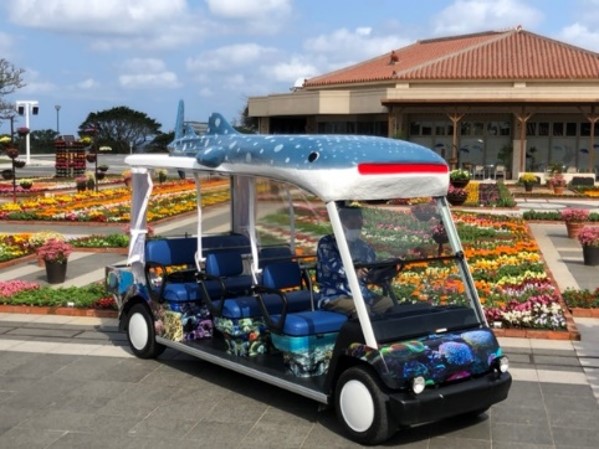
2.パーツスクリーニング
toDIMでは、AMアプリケーション開発において、
要件定義から設計、製造、品質管理までのトータルプロセスを支援しています。
要件定義フェーズでは、【パーツスクリーニング】と呼ばれる、
顧客課題・要望・サイズ・材質・必要強度等から積層造形に最適な部品を選定する作業を行います。
今回対象となる車体には、バンパー、タイヤ内側の足回り構造、シート、シート下側の電池搭載部・・・と、
多くの部品から構成されています。
この中から、従来工法では実現できなかった「軽量化」「剛性維持」「耐食性」等の課題を持つ、
フロントバンパーブラケットを選択することになりました。
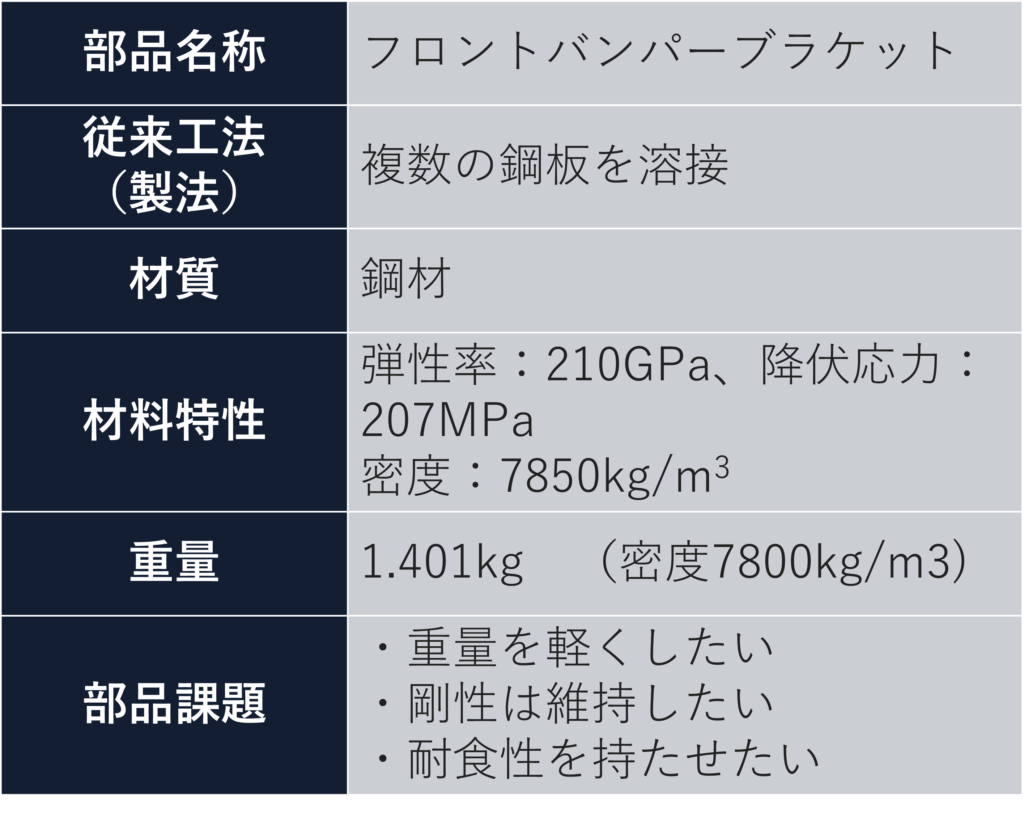
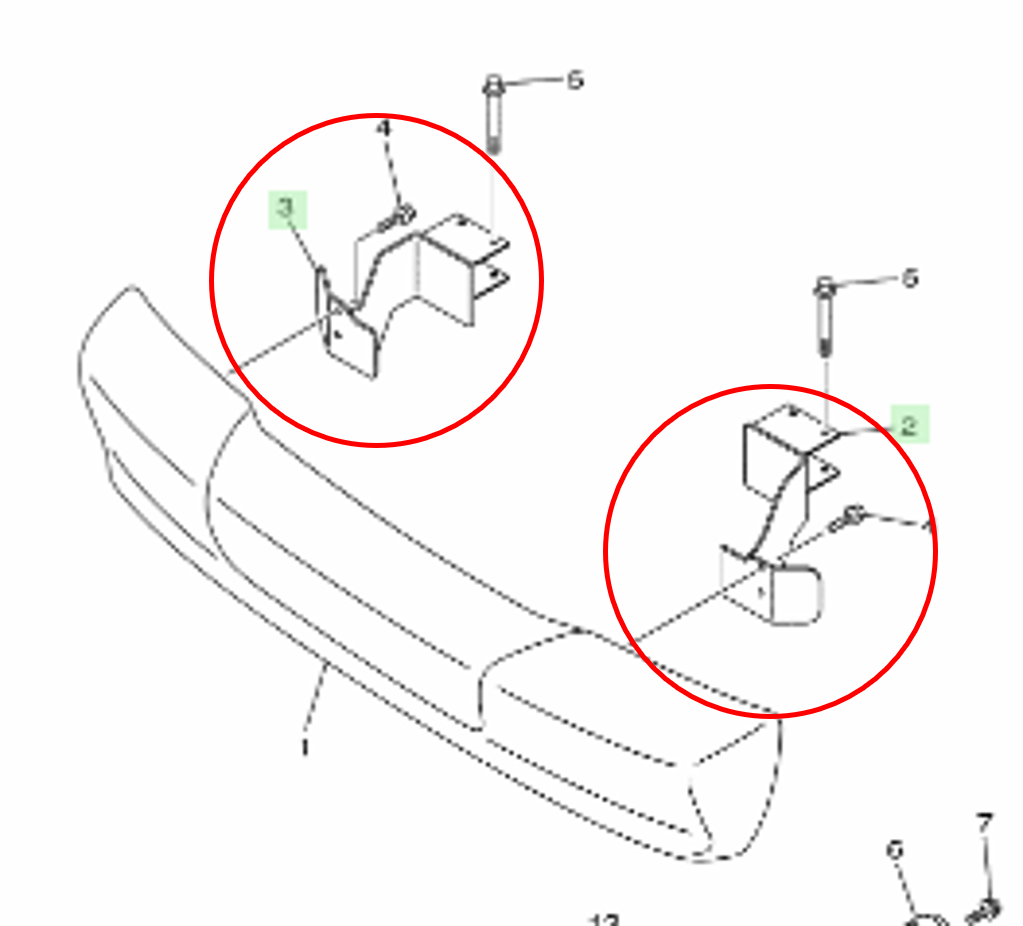
3.最適化設計(ジェネレーティブデザイン)
パーツスクリーニングにて選定した部品に対し、Fusion360のジェネレーティブデザイン機能で最適化を実施しました。
今回設計変更に使用するジェネレーディブデザインについて簡単に説明を行います。
使用するソフトはAutodesk社のFusion360です。
ジェネレーティブデザインは設計検討プロセスです。デザイナーやエンジニアは、設計目標とともに機能、空間条件、材料、製造方法、コストの制約などのパラメーターをソフトに入力します。
ソフトは、可能性のあるソリューションをすべて見つけ出し、設計案をすばやく生成します。
ジェネレーティブデザインではパラメーターごとに形状が出力されますので、その中からユーザーが形状を決定することになります。
次から実際に行った作業を工程ごとに説明していきます。
ジェネレーティブデザインに入力する材料特性や設計条件を現状モデルやヒアリングから確認します。
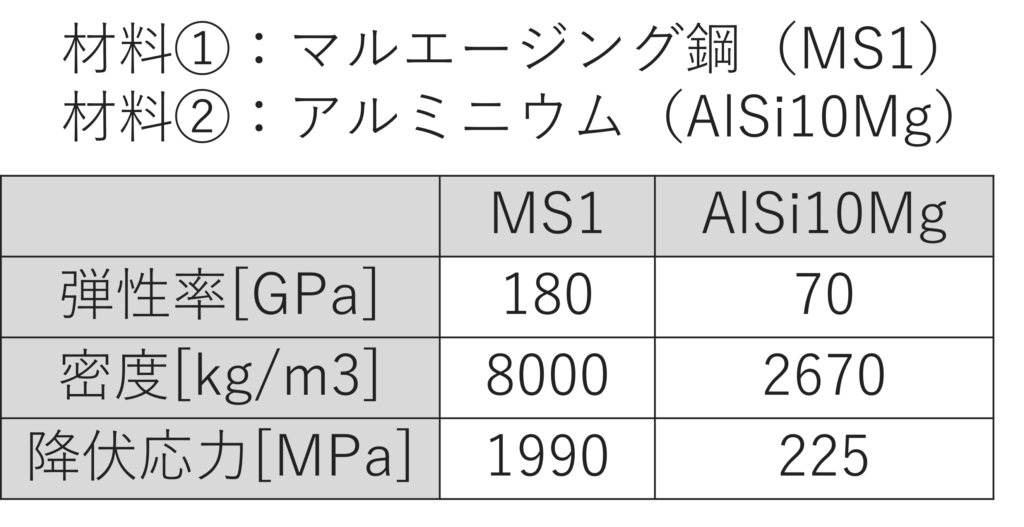
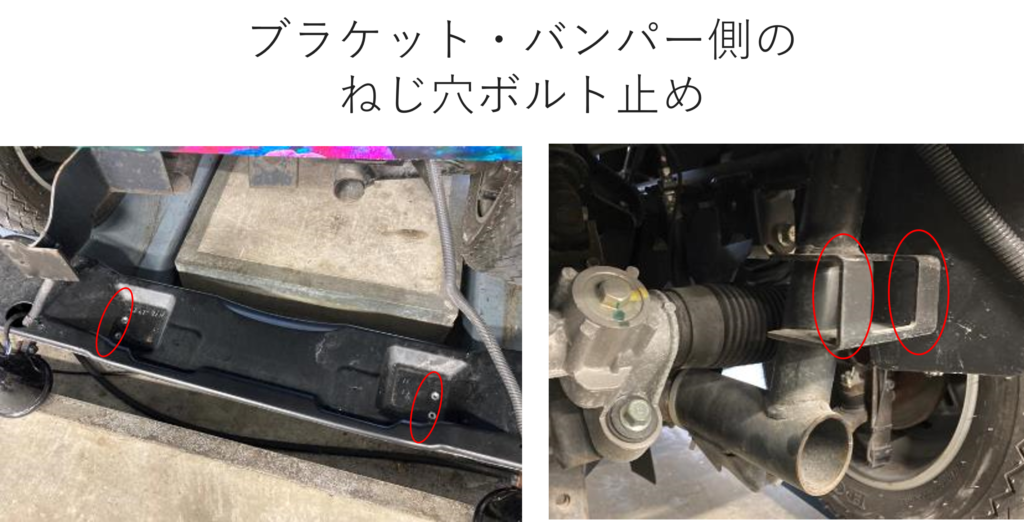
対象となる部品にかかる荷重・方向を決定します。
今回は、荷重条件として
・最高速度19km/hで障害物に衝突した場合に止まるまでの時間:2秒
・車体の質量:車体537kg+乗車5人(350kg)=887kg と仮定
・衝撃力 = (質量×速度変化)/衝突時間 の式より算出
= (887 [kg] × 5.27778 [m/sec] )/2 = 2340.7 [N] としました。
荷重方向としては、下記のような方向で設定しました。

車体・バンパーの後足部、ボルト通し部分を障害物(製品設計領域外)として設定しました。
今回は左右ブラケットは対象形状として、片側ぼブラケットのみを計算対象としました。
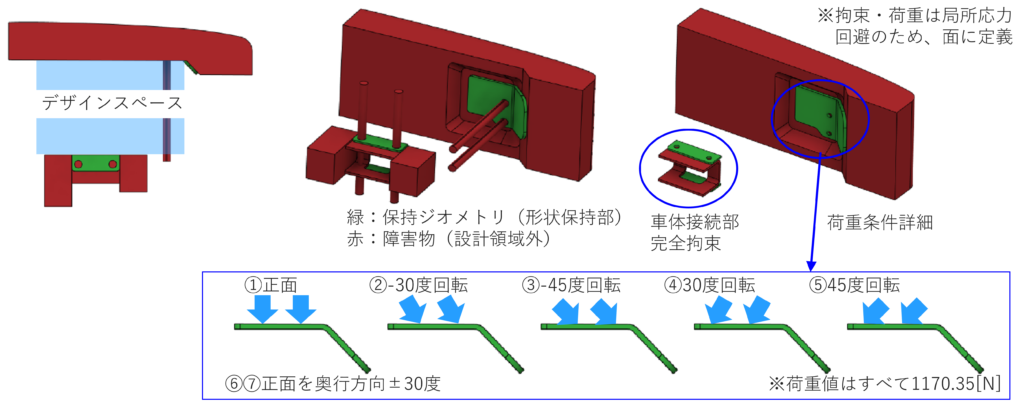
荷重条件、設計領域の設定が完了すれば、最後に目標・工法・材料の設定を行います。
・質量最小化
・剛性最大化
のどちらかを選択します。
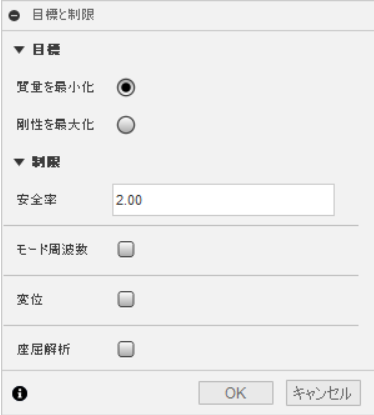
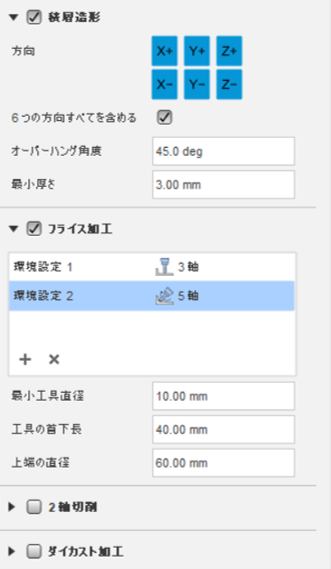
製造方法毎に材料を
選択します。
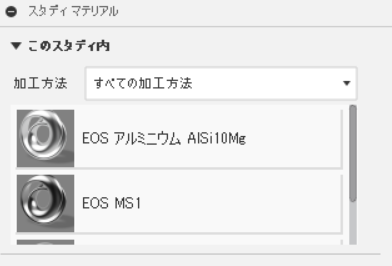
上記設定からジェネレーティブデザインの計算が開始されます。
計算はクラウドで実施されるため、ローカルPCのパワーに依存せずに形状算出が可能です。
設定した条件数により、複数の設計案が一度に生成されます。
形状や重量を確認しながら、設計案を選択します。
今回は、MS1(マルエージング鋼)とAlSi10Mg(アルミニウム)でそれぞれ一案ずつ選択しました。
ジェネレーティブデザインで出力された結果を見てみると、軽量化されていることがわかります。
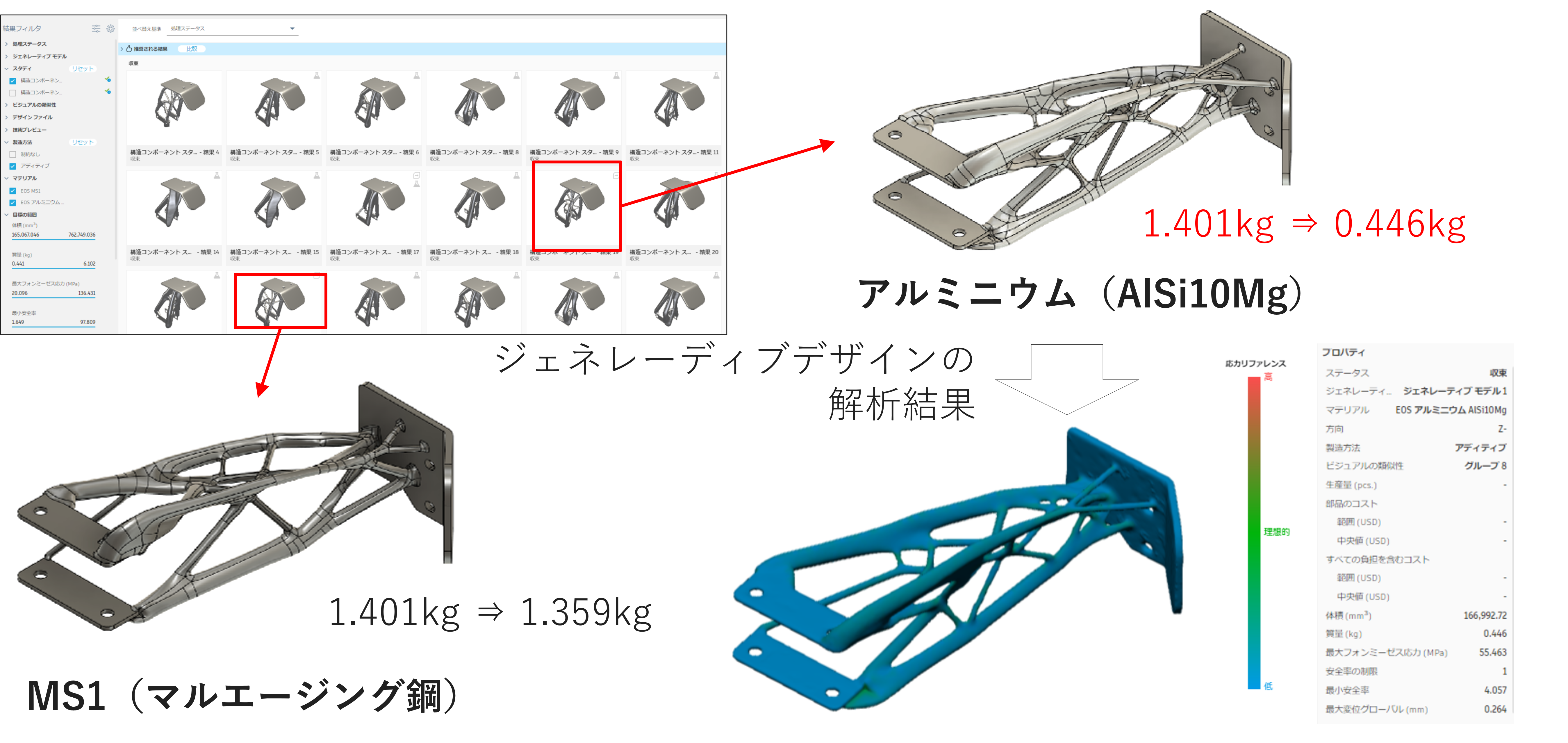
ジェネレーティブデザインで生成された結果を見ると、軽量化はされていますが、
応力等、荷重条件はしっかりとクリアされているのかを再解析をかけ、
いずれの形状も発生応力に問題がないことを確認できました。
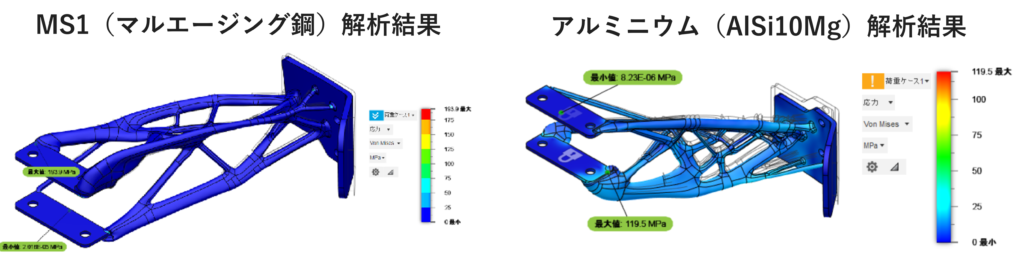
今回、AMだけでなく3軸加工(割り出し5軸)、5軸加工(同時5軸)での形状案も計算し、
下記の3つのモデルを造形・試作することとしました。
材料を従来の鋼材からアルミニウムに変更しても強度に問題がない形状を作り出すことができたため、
耐食性が向上する、アルミニウムを採用することにしました。
4.DfAM(Design for Additive Manufacturing):AMを活かす設計
ジェネレーティブデザインで計算された形状は、そのまま造形・加工するには難しい部分が存在します。
また、積層造形(AM)を行うにあたり、「積層造形のメリットを最大限に活かす設計:DfAM」が重要となります。
今回の形状に対しては、下記の修正を実施しました。
●サポートの検討:サポート材ができる限り少なくなるような形状の変更
●ジェネレーティブデザイン特有の形状変更:細い梁のような形状を修正し、少し太く修正
●造形ひずみ低減対策:造形時のひずみを低減するためのテクスチャーを付与
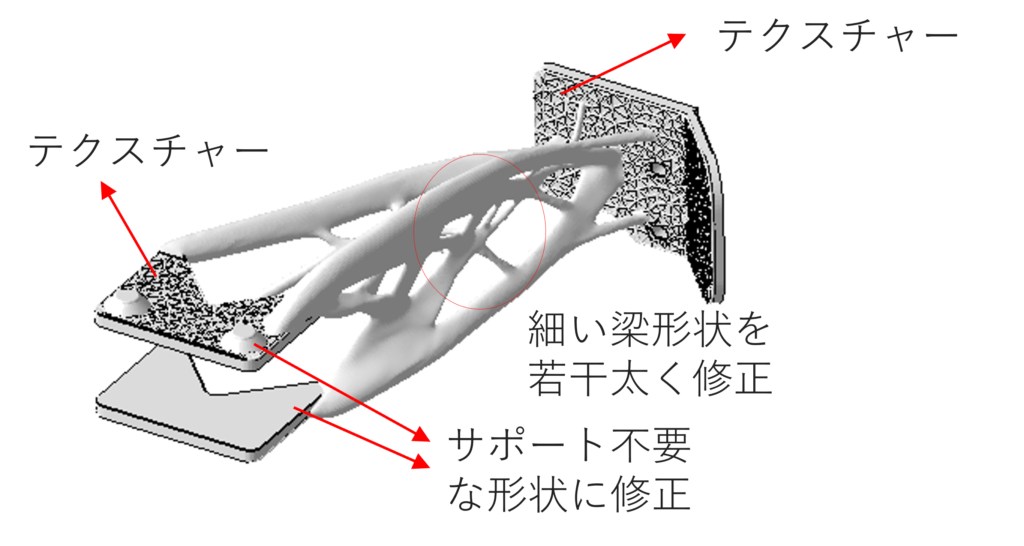
また、NetFabbにて、造形時サポート設計の結果比較・ネスティングのシミュレーションを実施しました。
オリジナルのサポート生成結果と比べ、DfAM実施後、サポート体積は約1/5となりました。
サポートの体積が減ることにより、造形時間・造形粉末費の削減に繋がります。
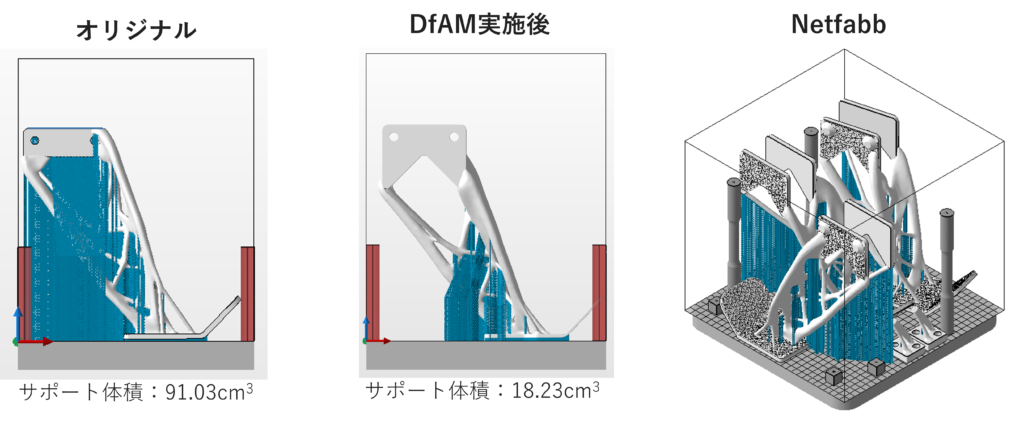
5.造形・切削加工・後処理
今回、toDIMネットワークのパートナーであるサービスビューロー様で造形を実施しました。
造形機はDMG Mori LASERTEC 30 SLMです。
切削加工に関しては、ものづくりネットワーク沖縄様で実施しました。
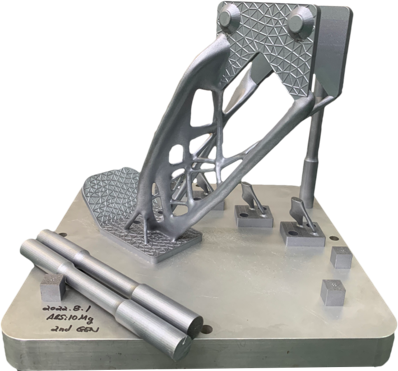
また、アルマイト処理もtoDIMネットワークのパートナー様で実施しました。
造形から後処理まで支援させて頂くことが可能です。
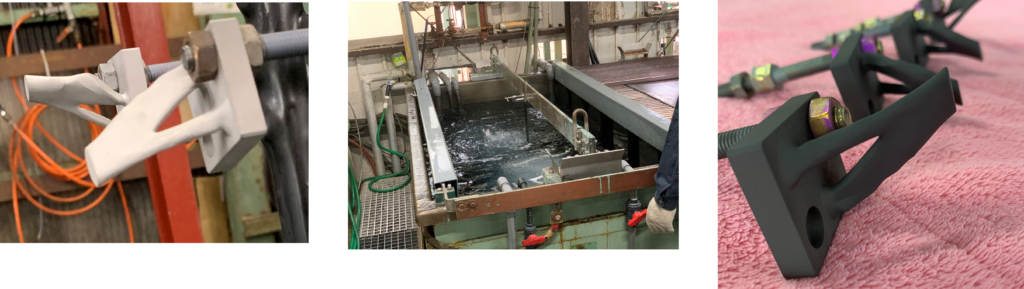
6.結果
今回の取り組みにおける課題解決の判定結果と詳細は以下の通りです。
掲げていた目標から大きく向上することができ、AMを活用した次のビジネスの期待に繋がる結果となりました。
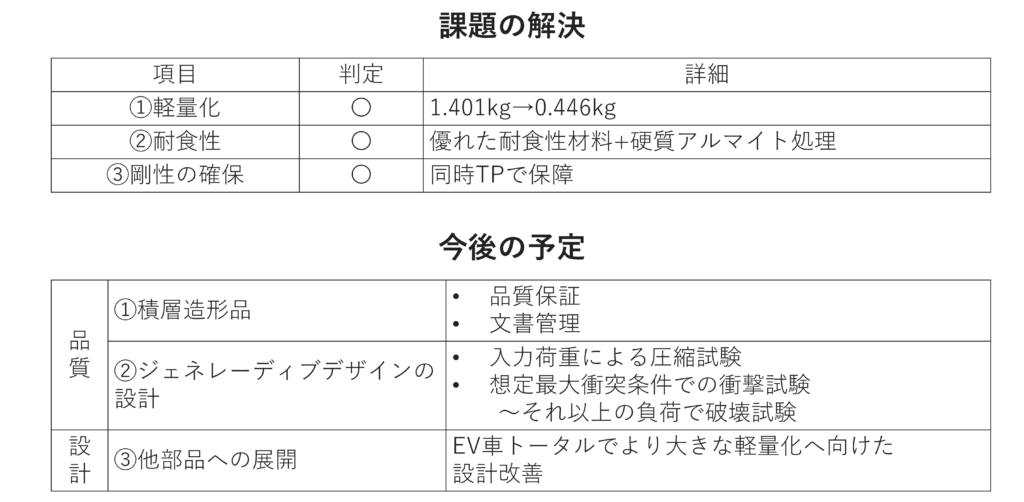
7.【追記】圧縮試験結果
・ 荷重-ストローク
・ ひずみ測定 (単軸、キーエンス社ひずみ計測ユニット NR-ST04)
・ 試験状況動画
※ひずみ測定位置は解析結果を参照
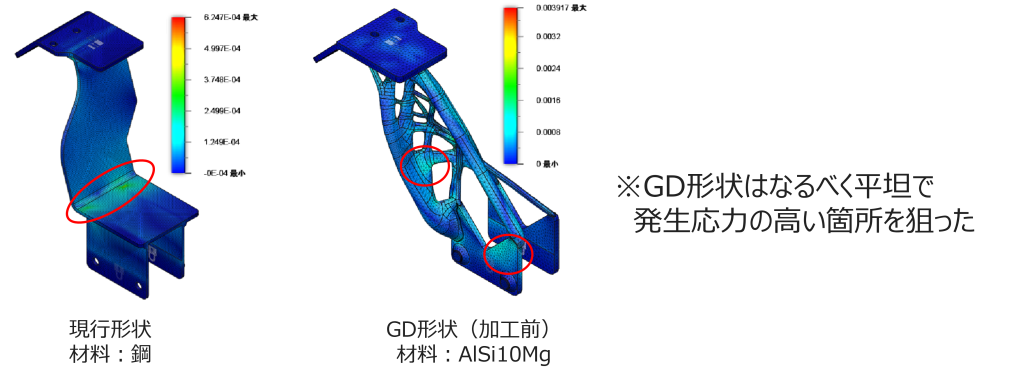
いずれの形状も当たってから押し込むまでの遊びが若干あった。(原因:加工精度・固定方法)
現行形状
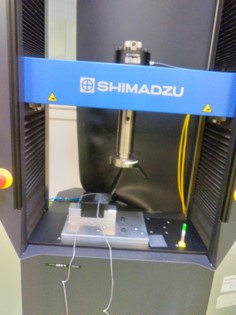
GD形状
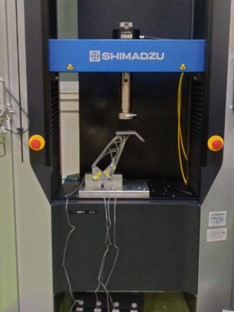
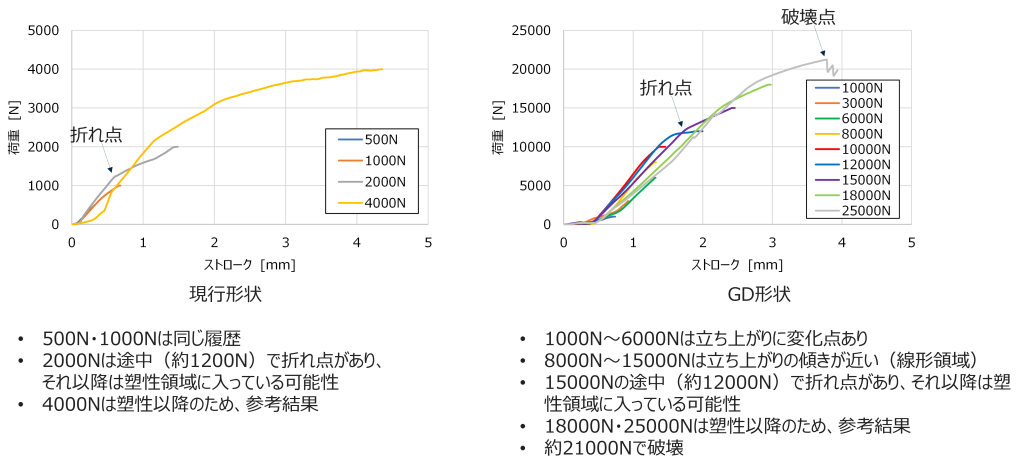
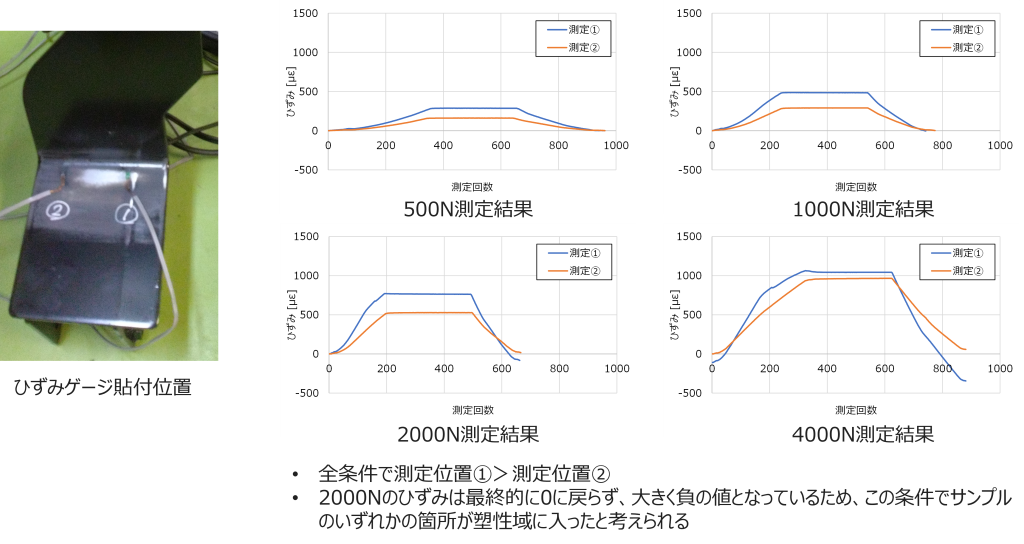
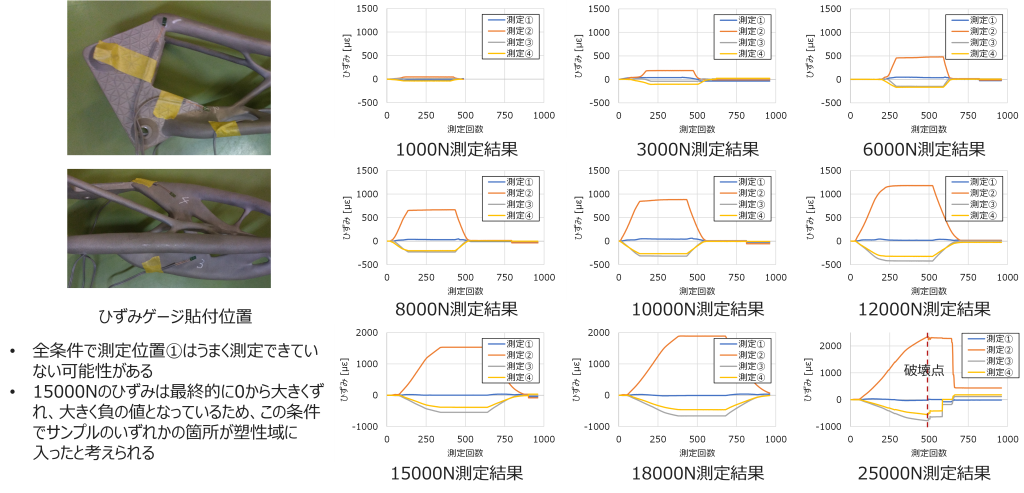