事例:株式会社吉松工機(部品開発:フェーズ03)
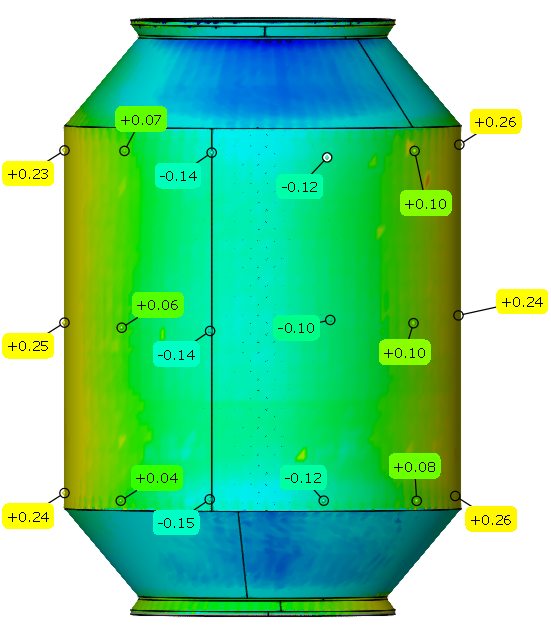
精密ロール部品のAM活用
ー軽量化や冷却効率向上に向けた取り組み事例ー
1.Phase02:生産化に向けた製造フローの検証および大型化への対応
Phase03ではPhase01・02の検証結果から得た最良条件を基準に大型化に挑戦。
以下がPhase3で造形した形状です。
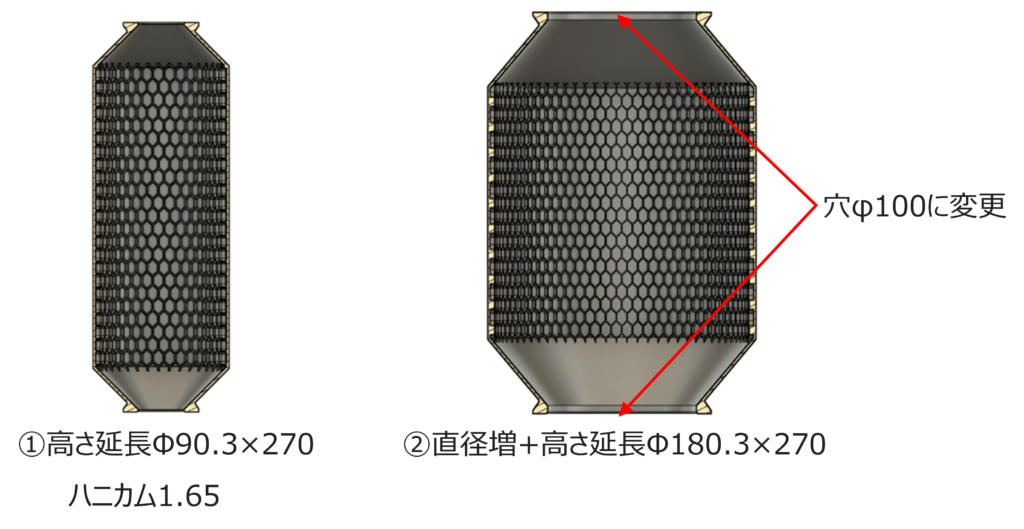
Phase3の金属積層造形は前回と同様、DMG森精機 LASERTEC 30 SLMを使用して造形を実施。
Phase3は2種類の検証を予定していましたが、造形スペースに余裕があったため、Phase4のモデルを1つ追加で造形しています。
3種類の造形モデルを以下のように配置し、造形モデル以外に強度試験の試験片、組織観察用の試験片を造形。
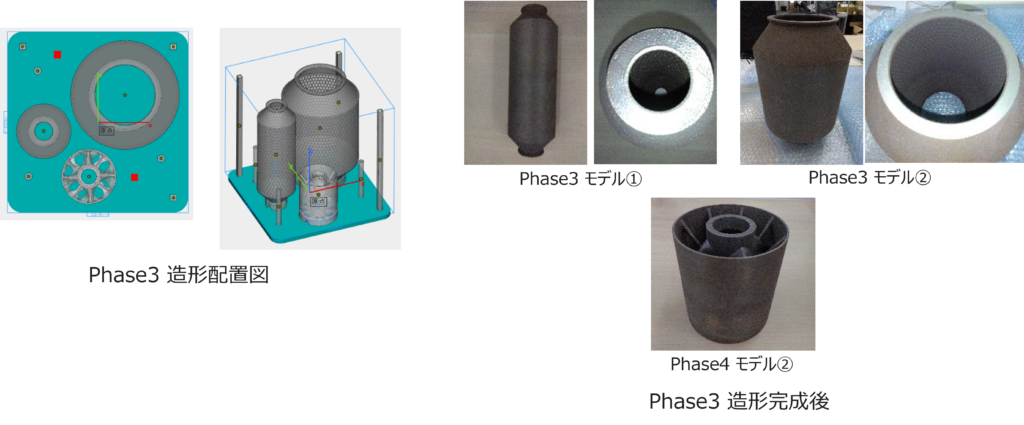
Phase3の寸法測定結果を以下に示します。
特にモデル①はCADとの寸法誤差が0.1mm以下と少なく、収縮率のチューニングが適切である結果であった。
また、造形時の熱歪みの影響もなく高精度で造形できている。
モデル②は径が大きいことから収縮率の影響を受けてしまい、真円度はモデル①よりも悪い結果です。
(チューニングによって精度向上は可能)
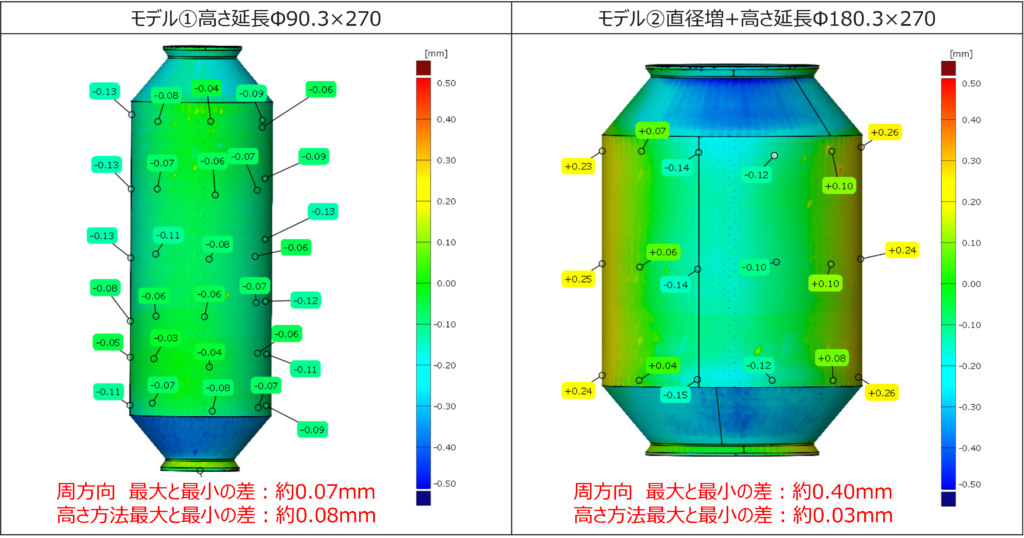
2.品質検査
Phase3の品質検査結果は以下になります。
本画像はビードの溶け込み深さを確認しています。
いずれもビード深さは充分であり、均一性もある程度見られることから、照射パラメータは良好であると判断。
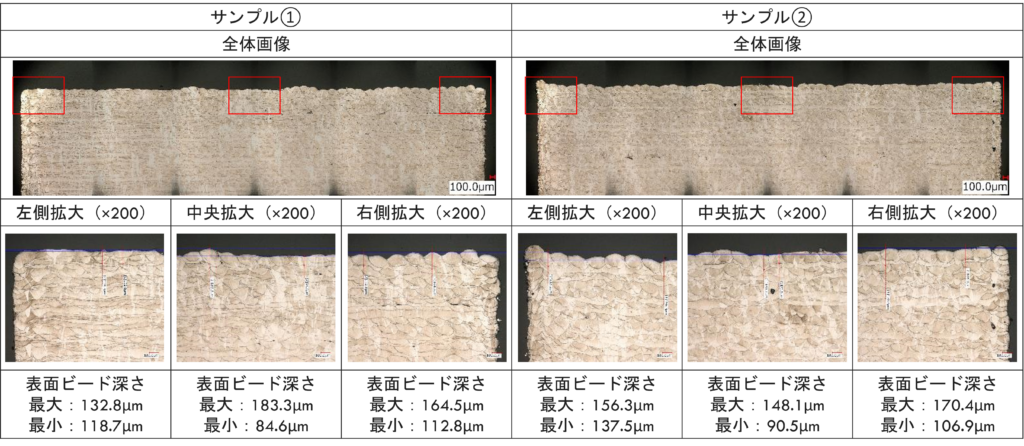
今回使用した材料はSUS316Lです。こちらの一般的な物性は引張強さ480MPa以上、弾性率197GPa、造形品では引張強さは550MPaとあります。
今回の結果は引張強さは規定以上の値となっていますが、弾性率が10%程低い値になっていますが、部品特性としては問題ないため、このままのプロセスで進めることとなりました。
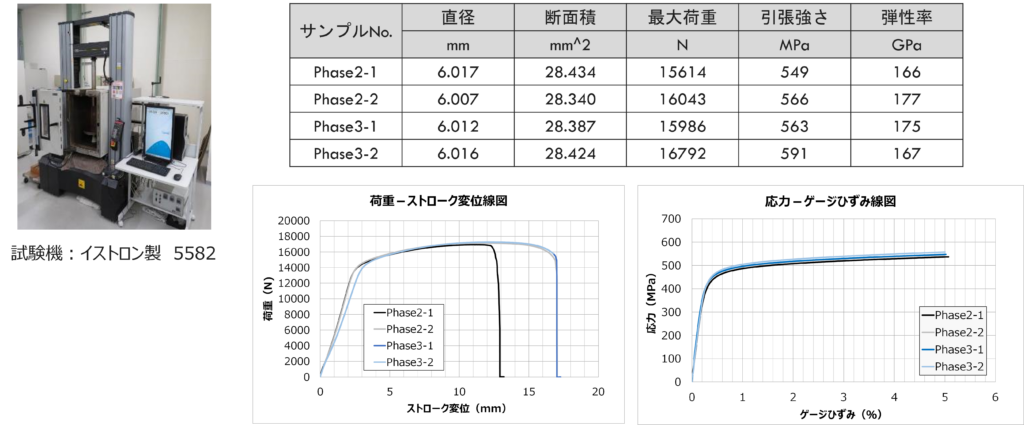
2.まとめ
・内部構造を設けることで、剛性が強く軽い精密ロールを製造できた。
・造形中の熱歪みの影響もなく、収縮率をチューニングすれば1/10mm以下の部品製造が可能である。
・ビード深さ及び大きな内部欠陥もなし
・径方向のサイズを大きくするためには、もう少しチューニングが必要である