事例:株式会社吉松工機(部品開発:フェーズ01)
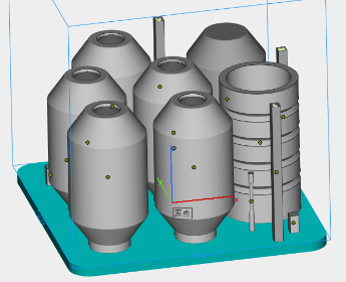
精密ロール部品のAM活用
ー軽量化や冷却効率向上に向けた取り組み事例ー
1.はじめに
株式会社吉松工機様は主に精密ロール、その中でも大型部品を得意とした企業様でございます。
長年培ってきた職人技術とAM技術を融合することで、現状抱えている精密ロールの課題解決や新たな付加価値を求めAM技術に挑戦されました。toDIMが過去に支援したフロントバンパーブラケット部品のテクスチャー機能を精密ロールに適用できれば軽量化へ繋がる可能性があると感じられ、AMの設計・試作・評価を開始いたしました。
今回のプロジェクトでは、精密ロールの軽量化に向けて最小肉厚の検証。それを拡大した場合のAM造形品の精度確認、他にもAMならではの付加価値を付けた形状も併せてPhase01~04と段階に分けて検討を実施し、AM適用の可能性を探ることを目的としました。
なお、今回のプロジェクトは造形の可否、造形品の精度や表面粗度、造形コストなど総合的に判断してパウダーベッド方式の造形で実施しております。
2.部品開発 ロードマップ
本プロジェクトは下記4つのフェーズと段階を分けて実施しました。
➊ソリューション導入:Autodesk製品(FusionとSimulationExtension)の導入とハンズオントレーニングの実施。
➋Phase01:軽量化を目標に後工程(研磨圧)に耐えれる最小肉厚を検証
❸Phase02:AM工法による製品付加価値を目指し、ジェネレーティブデザイン、二重構造、Textureを検証
➍Phase03:Phase01~02の検証結果から得た最良条件を織り込んだFIXデータの検証
❺Phase04:2024年機械用素技術展に向けた最終製品を製造
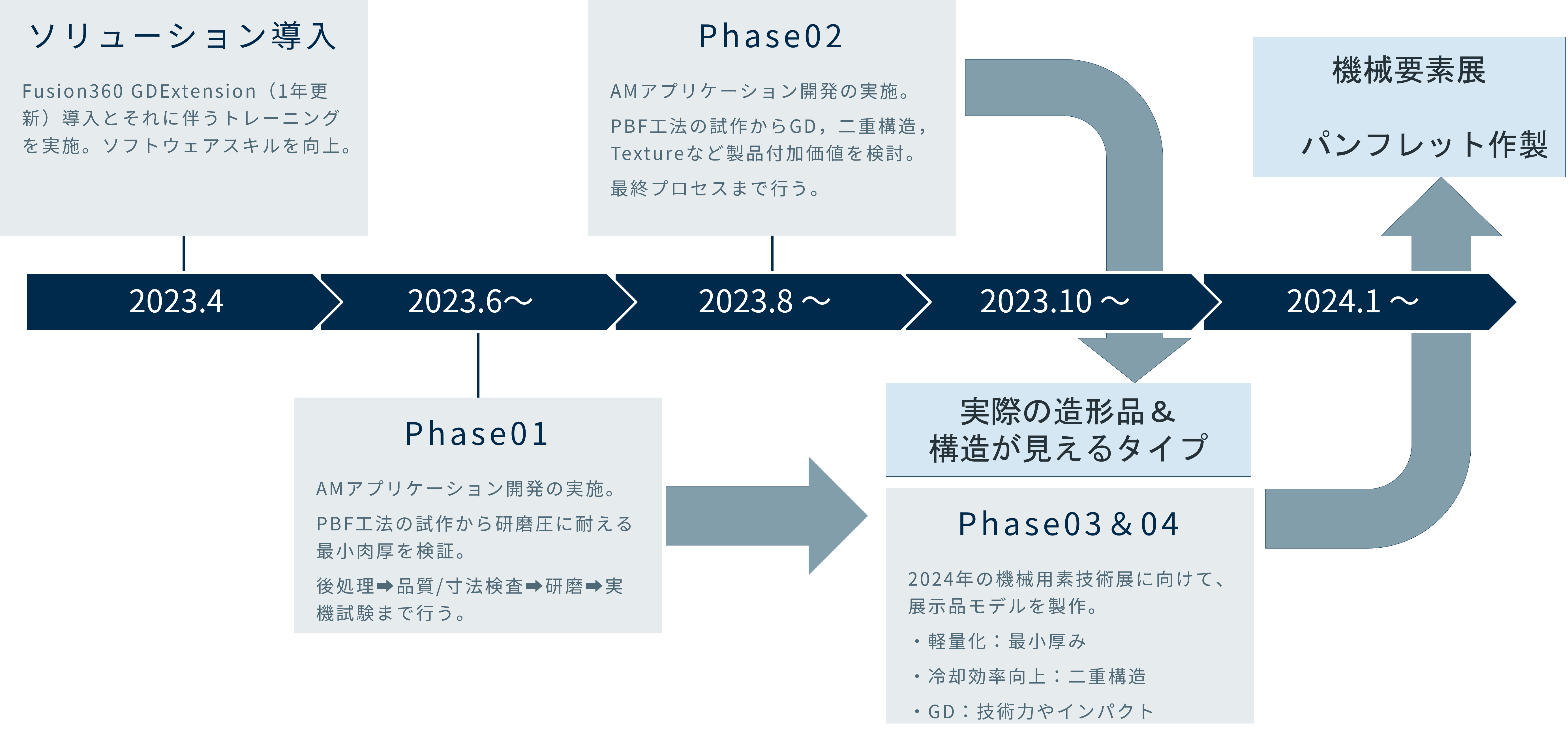
3.Phase01:軽量化を目標に後工程(研磨圧)に耐えれる最小肉厚を検証
基本形状を以下モデルとし、上下の傾斜部分は積層造形のデザインルールに沿って形状を生成。
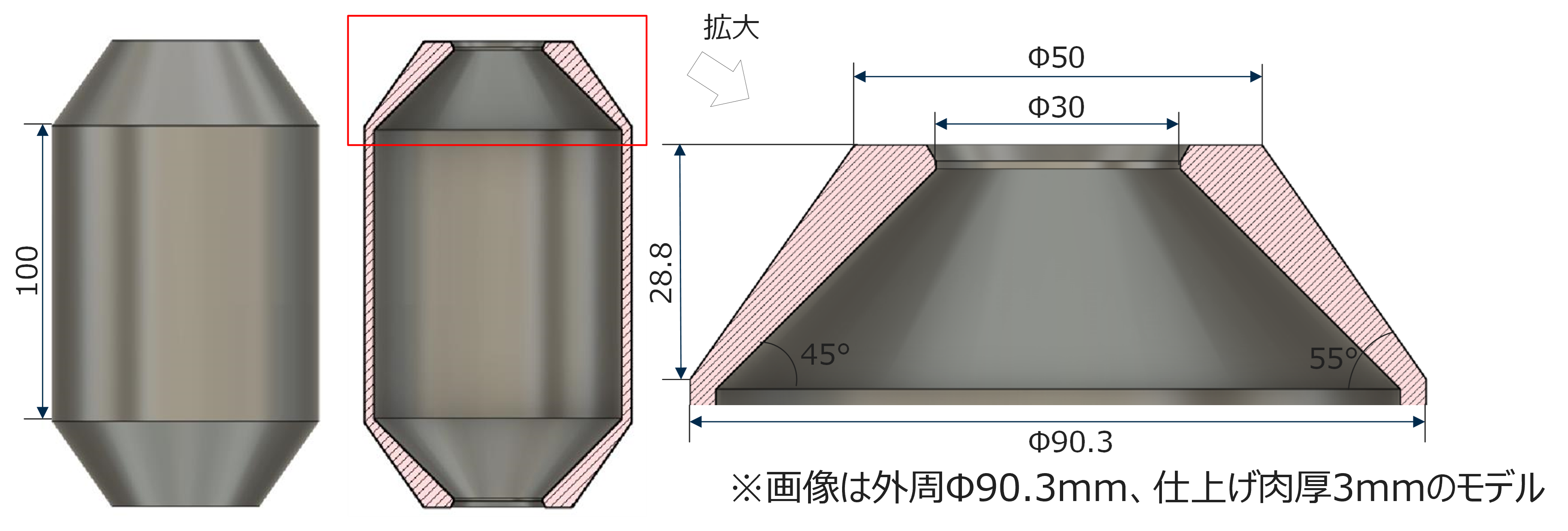
上記の基本形状から造形可能な7種類の形状を作成

Phase1の金属積層造形はDMG森精機 LASERTEC 30 SLMを使用して造形を実施。
7種類の造形モデルを以下のように配置し、造形モデル以外に強度試験及び品質検査用の試験片を造形。

積層造形後、ATOSを使用して寸法測定を実施
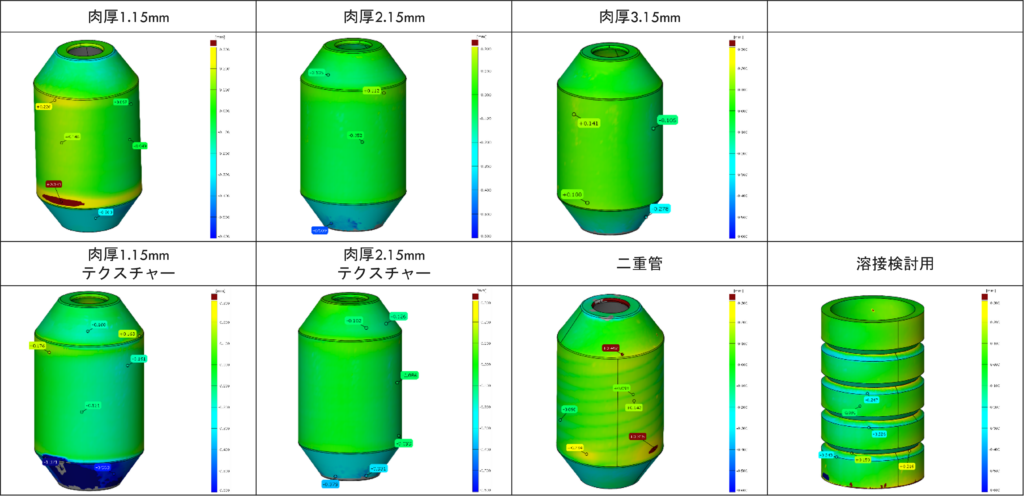
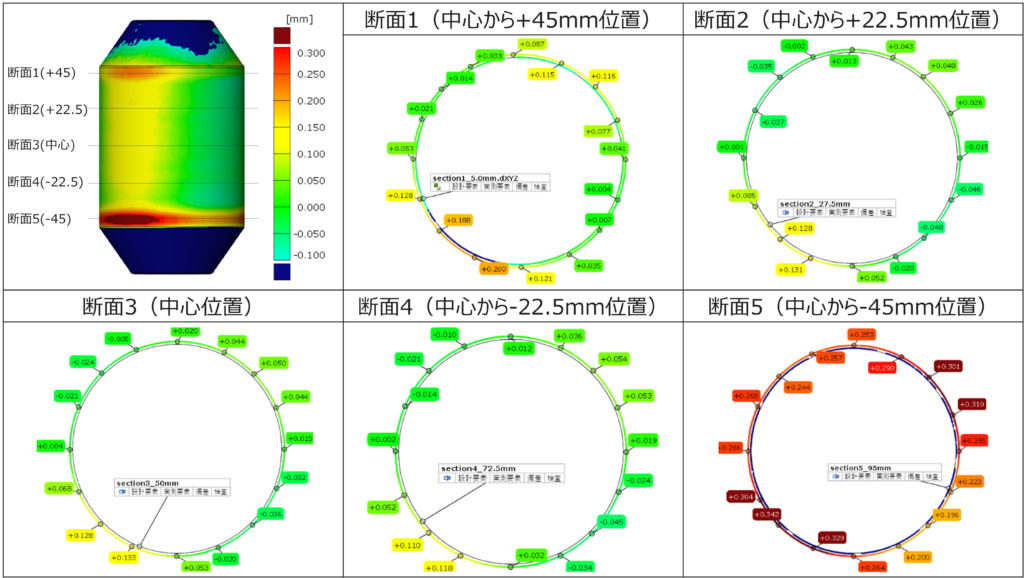
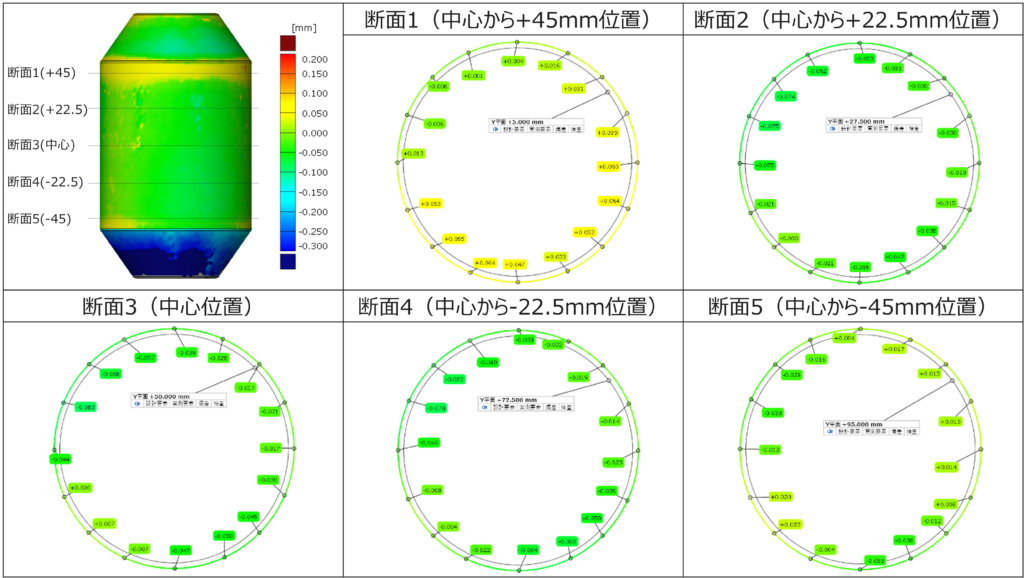
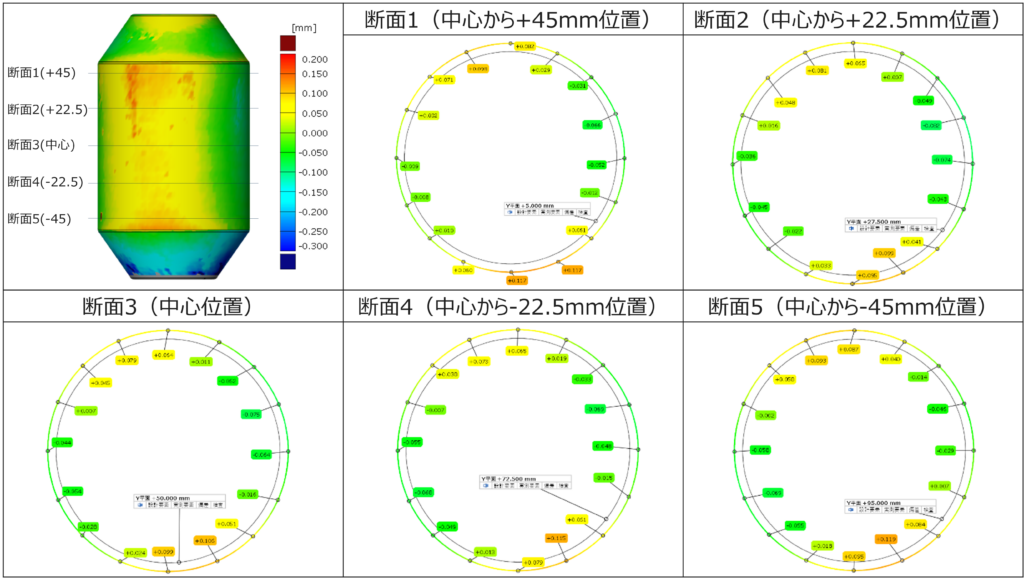
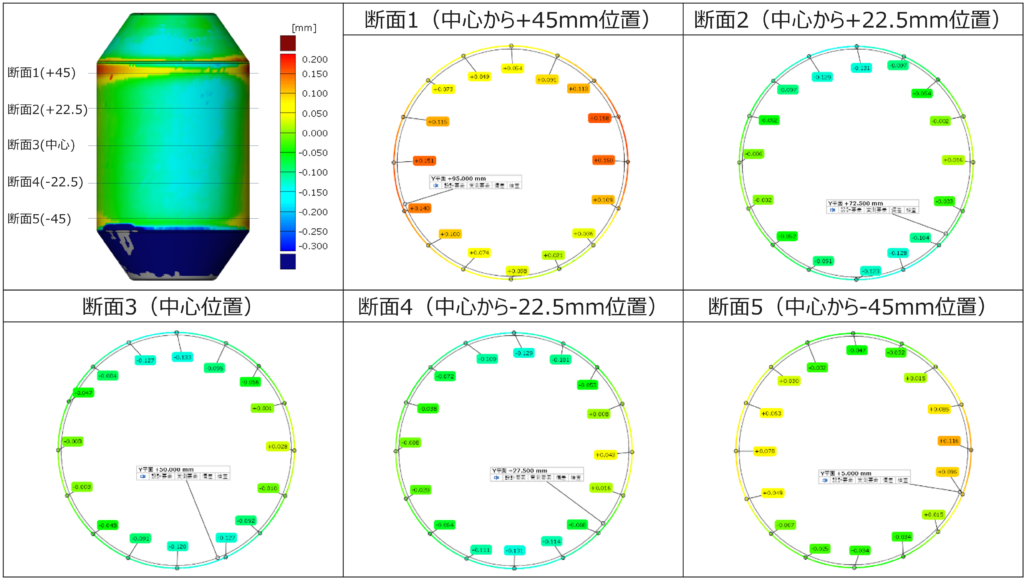
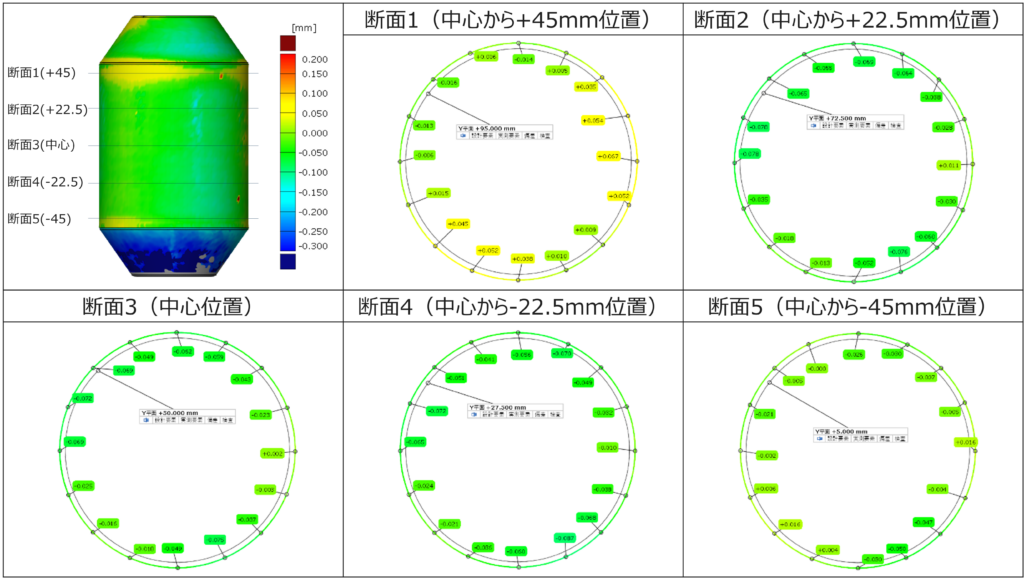
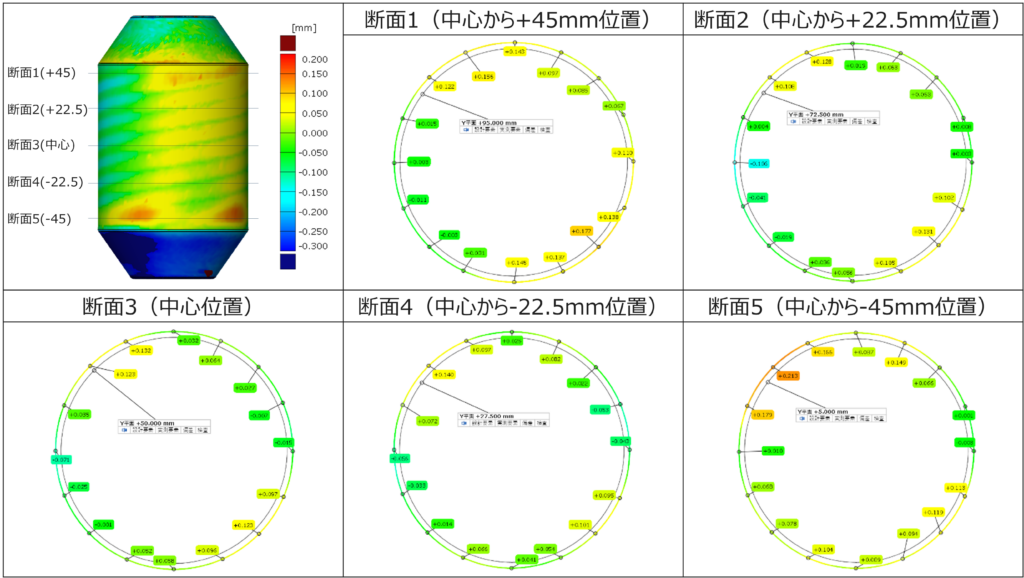
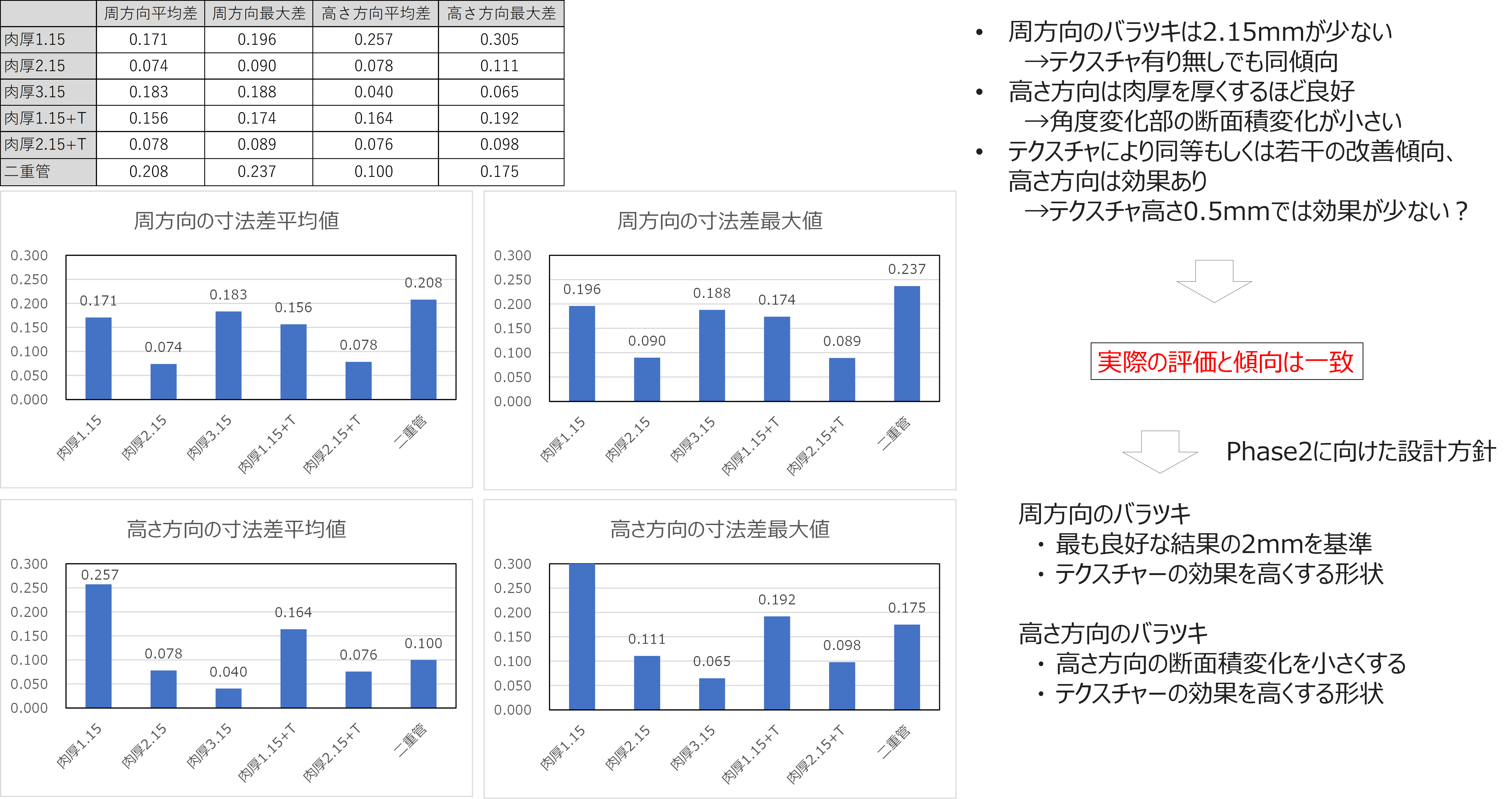
厚みによっては研磨工程で生じる熱や研磨圧に耐えれない可能性があるため、Phase01では研磨を実施。
4.まとめ
Phase1では肉厚3種類、そのうち2種に内部リブ追加、二重管、溶接確認用の7種類の精密ロールを造形しました。
•肉厚2.15mmが研磨工程を含めて最も良い結果である
•周方向の肉厚分布から、内部リブの剛性が不足している
•高さ方向の肉厚分布から、傾斜部と円筒部の断面積変化が大きいため歪みが生じている
様々な課題はあるものの、精密ロールのAM適用に向けて軽量化及び現状のコストと同等レベルで製造する可能性があると判断し、次フェーズへ進むことになりました。